ISO 9001 Quality Management System
August 14, 2024
13 min read
39What is ISO 9001?
ISO 9001 is the international standard for quality management. With the most recent update in 2015 – commonly referred to as ISO 9001:2015 – this internationally recognised standard governs Quality Management Systems (QMS).
A QMS is a collection of policies, processes, documented procedures, and records defining the set of internal rules that govern how a company creates and delivers products and services. ISO 9001 ensures that these elements, and ultimately the operations of the business, are under consistent and strict control so products and services meet a certain level of quality.
ISO 9001:2015 is designed to be compatible with other management systems such as ISO 14001 and ISO 45001.
ISO 9001:2015 applies to businesses in any industry and of any size. According to the International Organisation for Standardisation (ISO), there are over one million companies in over 170 countries which are currently certified to ISO 9001.
What are the benefits of certification to ISO 9001?
Here are some benefits of ISO 9001 certification:
1) Improves efficiency and reduces costs
ISO 9001 ensures your business is operating in line with the best practices in its industry. Compliant businesses use the latest technologies and processes. This means your work is more productive and efficient, ensuring your business is always staying ahead of the competition.
2) Provides independent, external feedback on your system implementation
Having an external third party audit the implementation and performance of your QMS is essential for picking up and remediating any gaps within the QMS and to ensuring ongoing continual improvement.
3) Provides formal recognition of your management processes for external stakeholders
The formal recognition of your quality management processes will also improve the relationship with your external stakeholders. Furthermore, it increases the chance of creating profitable partnerships.
4) Establishes customer confidence and provides your business with a competitive advantage
ISO 9001:2015 certification demonstrates your commitment to quality management, your expertise in the area, and your reliability in delivering a quality service. This helps your organisation stand out from competitors who are not ISO 9001 certified.
How ISO 9001 can help small businesses
For many small businesses, implementing a QMS and certification to ISO 9001 is a big decision. However, ISO 9001 provides small businesses with as many benefits as it does for big enterprises.
Being less complicated and more flexible are two critical benefits that small businesses have over the big ones, and if they use ISO 9001 correctly, it will have a significant influence on annual revenue and even make the difference between success and failure.
These are how ISO 9001:2015 can help small businesses overcome their biggest challenges:
1) Management
For small business managers, there is a lot to do on a daily basis. In addition to their expertise, managers might be dealing with other things such as finance, marketing, and relationship building.
All these day-to-day distractions can make managers more focused on short-term activities, and as a result, they may not have the time to spend on long term strategic planning for the business. A lack of long-term strategic planning is a threat to any small business.
Managers need to step out of their routines and think about how they can improve their processes, in a way that it requires less effort on their part so they can focus on more strategic aspects of their business.
ISO 9001:2015 can guide small businesses to implement a quality management system that enables them to meet and exceed their customer's needs.
2- Hiring Talent
Finding and hiring talent is one of the common challenges that small businesses face. Generally speaking, the challenge is caused by the below two reasons:
- Small businesses don’t have the brand name and resources of big companies
- Small businesses have not defined what they are looking for in a candidate
How can ISO 9001:2015 can help with this challenge? Implementing a QMS requires businesses to fully understand their context, objectives and how to get where they want to go. By establishing these things, businesses will better understand their own hiring requirements. Candidates will also see the vision of the organisation and understand how they can be a part of it.
3) Uncertainty
Change can bring about uncertainty for small businesses and this could come about at any time. Some examples of this include changes in the industry, or economy as well as changes with suppliers, employees or customers. The best thing to do is equip yourself with the right tools beforehand. ISO 9001:2015 could be what a small business needs in an everchanging environment.
The emphasis on interested parties and organisational context arms small businesses with all they need to know about the elements that have an impact on their outcomes. Risk-based thinking reveals different threats and opportunities, so small businesses have enough time to manage them effectively.
Common myths about ISO 9001
Business owners strive to earn profit to stay alive, but it’s not always clear which path leads to profitability. It’s not enough to have the instruments, technology or a team; it takes something more than that. You as a business owner should be able to implement a quality management system that results in consistent excellence. However, you might be concerned whether ISO 9001:2015 is the right decision for you or not.
Here, we explain how ISO 9001:2015 addresses some of the myths about ISO 9001.
1) More emphasis on leadership engagement
Myth #1 It's just paper on a wall
Top management shapes the strategic directions, sets goals and communicates them within the organisation. A QMS cannot fully integrate into the organisation’s strategic approach unless top management is committed to it.
When top management supports the QMS implementation, employees become motivated to engage in the process and feel more responsible. ISO 9001:2015, demands top management involvement to make sure organisations benefit from QMS results, including efficiency and customer satisfaction.
2) More emphasis on context of the organisation
Myth#2: It’s a single prescription for everyone
Context of the organisation is a new concept introduced in ISO 9001:2015. It includes all the internal and external factors that influence an organisation’s final product or service.
These factors make an organisation unique in its own way. With a complete understanding of its context, an organisation can implement a QMS in the way that is adapted to its specific needs and requirements.
3) More emphasis on customer satisfaction
Myth#3: It doesn’t influence the profit
Easy access to information and a wide range of alternative options have changed the way customers think and behave. They are looking to pay less and receive more value in return.
Most of the time, customers make their decisions about a product or service before even getting in touch with organisations. So you realise the fact that keeping customers satisfied might not be enough, you need to exceed their satisfaction.
ISO 9001:2015 is perfectly aware of this fact and pays more attention to customer satisfaction and ways to achieve it; the results directly influence the business profit.
4) Risk-based thinking
Myth#4: It’s not compatible with the high-risk environments
Risk-based thinking has always been in QMS implicitly, but now it’s more explicit. In ISO 9001:2015, risk is seen as a preventive measure in the whole process rather than something that comes at the end.
Risk can be thought of as all of the things that can go wrong within the scope of the QMS. Addressing risks helps organisations to prevent negative outcomes and be more proactive.
By determining risks at any stage, you can identify what elements or what parts of the process have more impact on your final results and then you can spend more time and resources to those parts.
There is no formal requirement to show how you are addressing risk in your organisation but doing so enables you to find and control deviations in your system in advance.
5) Less need for documented information
Myth#5: It’s complicated and needs lots of paperwork
The importance of organisational context and the rise of new technologies result in a flexible approach toward documentation. ISO 9001:2015 gives organisations the freedom to decide what amount of documentation they need based on their specific organisational context; also how they want to present those documents.
Documentation can be done in a range of different ways. Organisations can use web pages, videos, audio or any other form that is convenient for them. This way, the whole process becomes both simple and compatible with the organisation and its context.
Why ISO 9001 fails in an organisation
Certification to ISO 9001 might not always result in efficiency and customer satisfaction, but why is that? Here, we outline three main reasons that cause this:
1) Top management doesn’t get involved
ISO 9001:2015 asks for a significant amount of involvement from top management. When top management doesn’t participate, the QMS could turn into one of those side projects that only results in extra work and cost for the organisation and no one benefits from it.
2) Employees aren’t engaged
Employees are the biggest asset of any organisation, and without them, nothing gets done. They need to be involved in critical organisational processes such as the QMS. Top management should communicate the QMS objectives with all the employees. This way quality becomes everyone’s responsibility, and everyone has a specific part to do.
If this is not how organisations see the connection between people working for them and the QMS, they will not benefit from the implementation of a QMS.
3) Generic solutions are applied
If a generic solution is applied, either because the business sees a QMS as a just a certificate or check box, or because they have a limited understanding of the QMS this could result in failure.
ISO 9001:2015 states that knowing the context of the organisation is essential. Meaning, the QMS should be adjusted to suit the unique needs and features of your organisation.
To have a successful QMS, having knowledge of ISO 9001:2015 and its requirements is essential. It should be a strategic decision that comes from top management and involves all people in the organisation that could influence the implementation of the QMS.
Process
Certification can be an extremely valuable asset to organisations. It can enable them to attract more clients, generate higher revenue, and build better customer confidence. In addition to this, some organisations require businesses to be certified to management standards in order to win tenders.
We specialise in assisting organisations with developing and implementing management systems which put your business on the path to becoming certified.
Our 8 Step Process is designed to give clients the most efficient turnaround time whilst delivering service that is second to none.
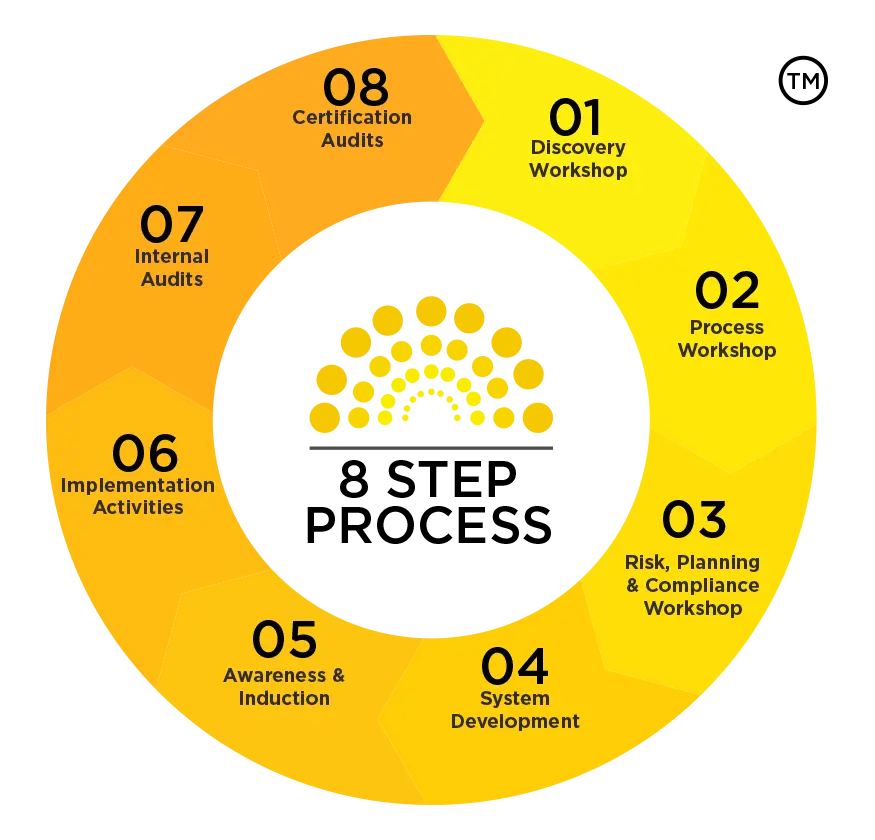
What does an ISO certification body do: Stage 1 and Stage 2 with audit certification body
Third Party Certification is the process of having your Management System audited by an independent third party. This type of auditing is typically used by Conformity Assessment Bodies (CABs) who are regulated by a government organization known as JAS-ANZ. These CABs can issue registered certificates of compliance to various standards such as ISO 9001, ISO 45001, and ISO 14001.
Stage 1 and Stage 2
The formal assessment process includes two stages. In stage 1, the auditing body will confirm whether you have met the requirements of your proposed scope and the objectives you have set for yourself. If there is any kind of minor or major nonconformities, you will have some extra effort to put in.
The auditing body will give you some time to address the nonconformities, before beginning stage 2 of the audit. In stage 2, your system will be assessed again to make sure that all nonconformities are corrected.
At this point, if there are no major nonconformities, your certification can be issued; otherwise, you will be given time to correct existing nonconformities before the next visit of the Auditor and only after removing all the major nonconformities your organisation will be eligible for ISO 9001 certification.
Surveillance Audits
Typically, the certification body will do yearly surveillance of your management system for the first three years after your certification is issued. This ensures your organisation continues to meet the requirements of ISO 9001 after certification has been achieved.
Frequently Asked Questions
As a leading provider of consultancy services we cover a wide range of disciplines including quality compliance, safety compliance and environmental compliance across high-risk industries.
ISO 9001/Quality Management Systems are applicable to all industries and areas; the key ones we work with include high risk industries such as construction, manufacturing, aviation, professional services, healthcare, and transport.
A Quality Management System alone won’t add any value to your business or your staff. If the Quality Management System is designed to fit into the existing operations of the business, and with input from the expected staff who will be using the system, then you will start seeing improvement.
You can expect the following improvements from implementing a Quality Management System:
- Less instances of the organisation quoting/tendering for a project/client that they cannot actually provide the product or service for
- Better responses to customer complaints
- A mechanism for identifying issues and then systematically fixing them and preventing them from occurring again
- If certified, recognition from your customers for achieving certification and increased confidence from prospective customers
These are some of the benefits of a Quality Management System although there are many more that an organisation can achieve if it adopts the system into its core operations.
Third Party Certification is the process of having your Management System audited by an independent third party. This type of auditing is typically used by Conformity Assessment Bodies (CABs) who are regulated by a government organisation known as JAS-ANZ. These CABs can issue registered certificates of compliance to various standards such as ISO 9001, ISO 45001, and ISO 14001.
Unlike many competitors who operate by a time and materials model, we operate by a fixed-fee model. We provide clients with proposals that outline the methodology for the project, the deliverables, and the total cost.
Separately on your end, you'll need to engage the external third-party certification company whose cost will be in addition to our cost. We can definitely put you in touch with certification companies.
Yes, the initial consultation meeting with you to gauge what certification would be suitable for the business and also get an understanding of how the business works is free so that we can provide an accurate proposal.
4-6 months (client preparedness plays a major role here).
If there is a tender or client demand for urgency, we and the Certification company can write you a Letter of Commencement, upon request.
Why Compliance Council?
Compliance Council are compliance consulting experts for high-risk industries across Australia. As a leading provider of consultancy services, we cover a wide range of disciplines. These include safety, quality and environmental compliance across all high-risk industries. Our team of professionals have significant experience gained by working with companies of all sizes, ranging from startups to multinational corporations. The need for compliance in Australia is becoming increasingly prevalent, especially given the high standards and demands placed on businesses and providers of goods and services. Compliance Council strive to take the burden and stress of meeting these industry standards, in what can often be a time-heavy obligation for time poor industries.
Contact us today to discuss how our experienced consultants can assist your organisation with achieving ISO 9001 certification.
Contact UsSign up for our newsletter
Stay Ahead: Subscribe for the Latest Compliance Insights and Updates.
We care about the protection of your data. Read ourPrivacy Policy.